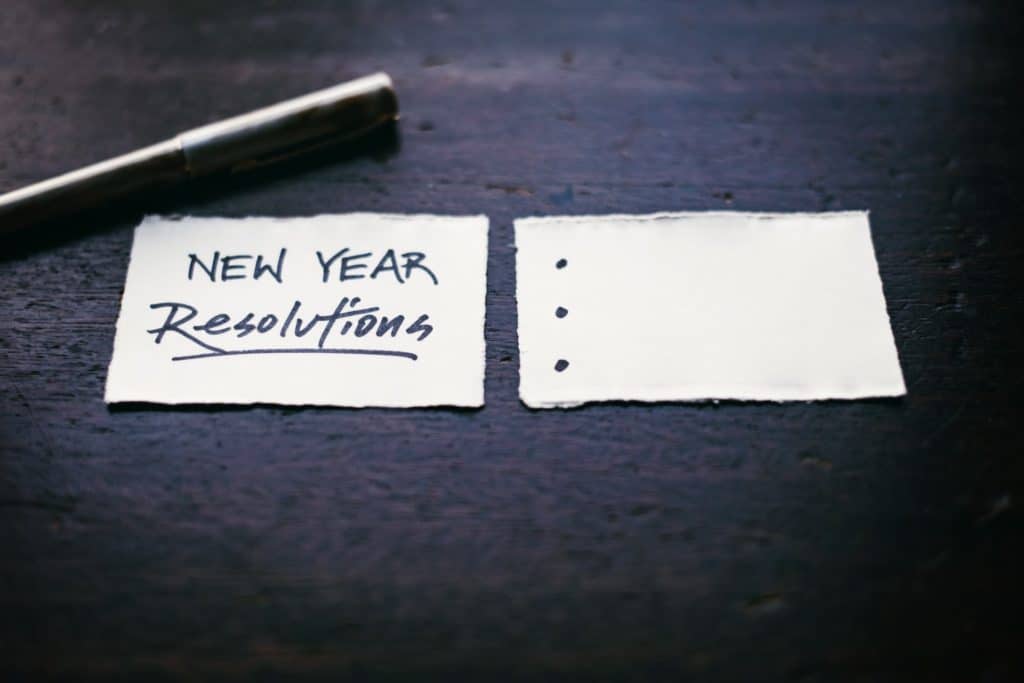
Whether you’re in the beginning of your Lean journey or simply eager to start, early 2022 is the perfect time to learn some best practices.
Lean manufacturing processes will help you reduce waste, increase productivity, and shatter your profit goals.
The Lean manufacturing consultants at Campbell Corp. recommend these New Year’s resolutions for Lean process improvement.
These simple, easy initiatives are a great way to begin or kick start your Lean journey.
Remember, Lean is continuous improvement and is comprised of the accumulation of small steps which result in big change. These are the perfect way to start.
Resolution 1: Implement a 5S Project
Simply, the 5S’ of Lean are:
- Sort
- Set in Order
- Shine
- Standardize
- Sustain
Begin with Step 1, Sort. Get rid of unneeded inventory, fixtures, tooling, and equipment. If you infrequently use a tool or fixture, remove it from the shop floor. If you haven’t used it in years, recycle it.
Make certain that aisles, walkways, stairways, and areas in front of electrical panels and shut offs are free of stored items. If needed, host a Red Tag Event. Remove everything from the floor and only keep items which your operators retrieve after a week or month in the work area.
Resolution 2: Identify Your Constraints
Your largest constraint is likely clearly apparent you just have to look for it. It’s the process or equipment with the most Work in Process in front of it.
Taking steps toward Lean process improvement means identifying this constraint and taking steps to address it.
Resolution 3: Measure and Track a Component of OEE
OEE is short for Operational Equipment Effectiveness and is a simple formula which measures your health as a manufacturer:
OEE = Availability x Performance x Defect
Availability is a measurement of how often your equipment is actively transforming raw materials into finished goods. Beaks, change overs, planned maintenance, and unplanned repairs erode your manufacturing capacity.
Take initiatives to increase Availability by staggering breaks and operating throughout a shift, reduce change over times, perform preventative maintenance, keep an inventory of wear items and consumables, etc.
Performance measures equipment efficiency and takes into account cycles which are not performed at equipment capacity due to short stops not captured in Availability or any reason your equipment is operating slower than capacity.
Challenge any preconceptions limiting the Performance of your equipment and when and where practical work to decrease your cycle times.
Quality is arguably the largest of the 8 Lean Wastes because it contributes to multiple wastes possibly including Over Processing, Excess Motion, Transportation, Waiting, Over Production, and Excess Inventory. Improve your Quality and you will naturally improve your performance.
Resolution 4: Pilot Single Piece Flow
Single Piece Flow allows for the production of product when it’s ordered. While it’s not for every manufacturer, it’s the gold standard of manufacturing and is considered world class.
Implementing it in an existing operation, however, can seem overwhelming and fraught with risk. Try taking two or even three adjacent operations and converting them to Single Piece Flow. This will involve equalizing the work content, redesigning the work areas, and implementing a materials plan to support the new processes.
Resolution 5: Host a Kaizen
A Kaizen Event shouldn’t be intimidating. It’s simply a short, focused event to improve a process or implement and initiative. It involves Pre-Work including defining the event, scheduling it, and assembling the team as well as performing any required supporting research or data collection. The event itself should be structured and post event activities should be defined with responsible parties, a schedule, and a budget if necessary.
Consider hosting a Kaizen Event to 5S your facility, relieve a constraint, improve your OEE, or pilot Single Piece Flow.
Resolution 6: Communicate with Your Operators
If you’re already not regularly communicating with your operators, make 2022 the year you open communications with the worlds subject matter experts on your operations. Listen to their concerns and suggestions. Lean has a tool to promote communication and it’s called a Gemba Walk. Traditionally, Gemba Walks are performed at the same time on a daily basis and are meant to not only provide management visibility of their operations but to foster communications between operators and decision makers.
Resolution 7: Start a Lean Library
There are some fundamental books available for purchase which at least some of your employees will avail themselves of. Give them the resources to educate themselves and become your advocates for Lean.
Resolution 8: Hire a Lean Consultant
Hire a Lean Consultant to improve your manufacturing health, capacity, and profitability while reducing your lead time and defect rate. Lean can be black and white and much effort can be spent on low impact initiatives. A qualified and experienced Lean Consultant can help you navigate Lean to leverage the Lean tools and techniques to quickly see the results which achieve your operational goals.
