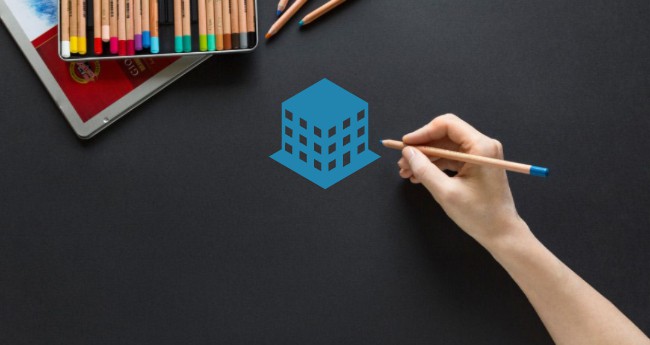
The facility layout is a critical part of running an efficient industrial plant. It determines flexibility in terms of future expansion or change, handling of materials, and the planning of the output needs of the facility.
It is critical to optimize the facility design layout for the organization to run effectively. Facility layout can be defined as the arrangement of different aspects of the manufacturing process. With a good layout plan, it is possible to optimize the flow process to get the desired results.
Factors Determining Facility Design and Layout
Manufacturing plants in different sectors tend to have varying designs depending on what they produce. Each plant has the task of determining which arrangement will yield the best results for their process. There are a few factors that may influence the type of manufacturing plant floor plan an organization chooses.
- Overall Objectives: Before adopting any strategies for process improvement, the overall objectives of the organization must be considered. Some businesses may want to optimize their space, while other plants may require a better system for safety.
- Future Plans for the Organization: The process design and layout should incorporate the plans of the organization. The organization’s objectives will determine how future expansion of the plant will be accommodated.
- Space Utilization: The direction of the pathway, the movement of the materials, and the information flow are some of the critical elements that must be considered if space is to be optimized.
- Safety: The plant should have a process flow that is safe and reduces the risk of hazards. But safety precautions should not compromise the flow of the process.
Layout Problems and Principles of Lean Manufacturing
Many industries continue to adopt technology at an increasingly rapid rate. Organizations are now faced with new challenges when determining the type of facility design. Manufacturing plants today, need to continuously optimize their efficiency, reduce costs, and still produce quality products.
When developing a structure for facility design, it is crucial to observe manufacturing principles that will optimize the plant and keep it productive. Some of the principles include
- Flexibility: The facility design must anticipate the possibility of future expansion. As technology changes rapidly, organizations must structure their systems to keep up with new developments.
- Capital: The capital investments should be kept at a minimum when developing layout plans. Costs can be checked with the proper utilization of space, manpower, and machinery.
- Nature of Flow of Movement: Depending on the industry, the plant there are varying process flows that the plant may adopt. The aim is to ensure that there is no conflict when materials are being exchanged across the floor. If the pathway has bottlenecks, coordinating information and personnel can soon become virtually impossible.
Boosting Employee Morale
The psychological well-being of the staff at the plant is vital for productivity. The factory layout should, therefore, incorporate elements that can boost the motivation of the employees. These elements could be simple additions such as better lighting or more appealing colors on the walls. They could also be more extensive such as building a cafeteria or gym.
Bottom-Line
Lean manufacturing principles have been applied in industry for decades. But in recent years, organizations are faced with challenges that come with rapidly changing industries. If facility design is considered carefully with these challenges in mind, industrial plants can create quality products, reduce costs, and boost morale.
