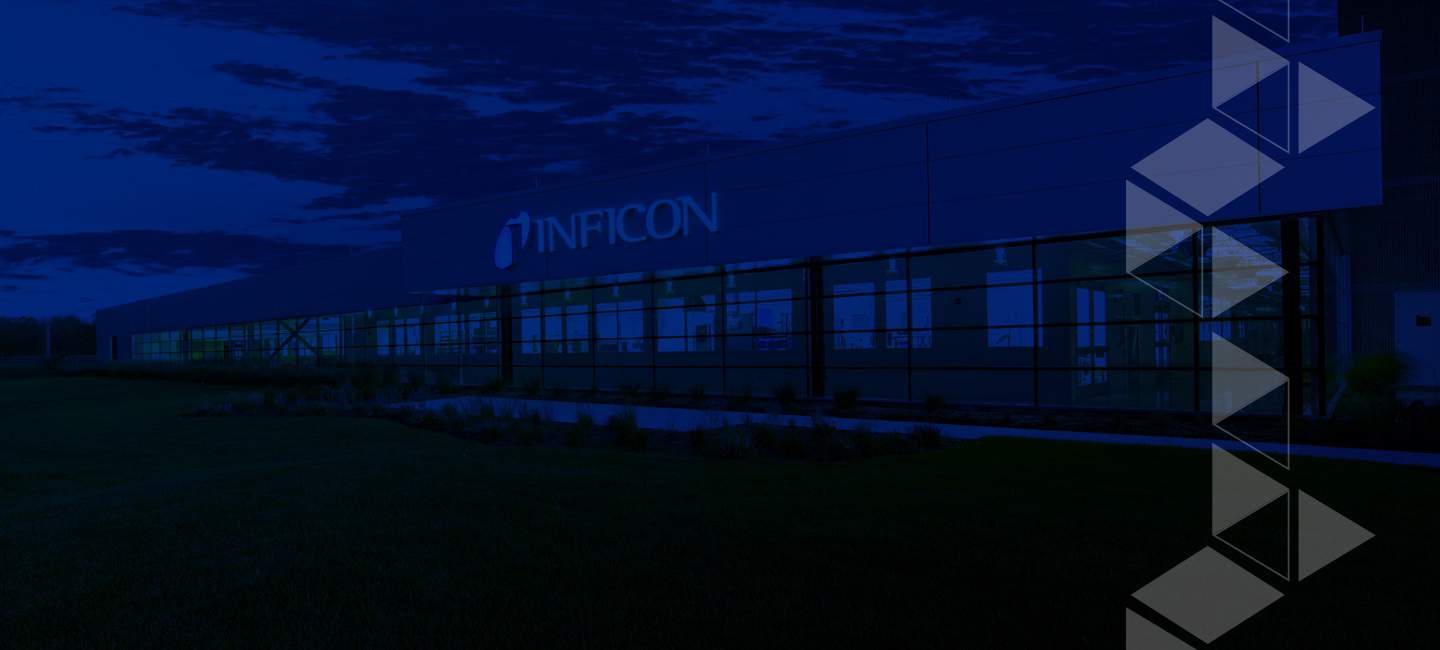
Case study:
Inficon
Manufacturing Facility Growth Spurs Expansion
World-Class Manufacturing Plant Relocation
INFICON, a Swiss-based company with world-class manufacturing facilities in the United States, Liechtenstein, Germany, and China, had seen impressive financial growth since building their existing facility in Syracuse, New York nearly 25 years prior. In that time period, the Syracuse-based division of the international tech company had seen sales quadruple and future projections showed their growth potential would only continue. Leaders of the company knew that it was time to expand the facility but questioned whether they could expand upon the footprint of their existing space, or if a new location was required to meet their future manufacturing needs. Additionally, INFICON wanted to maximize their investment by ensuring their new facility not only gave them space for future growth but best utilized the new space to bring greater efficiencies into their operations and processes.
To answer these questions, INFICON conducted a nationwide search for a partner that could help them realize the best solution for the potential manufacturing plant relocation and expansion. While the firm ideally wanted to partner with a local consultant, INFICON ultimately chose Campbell Corporation because of their unparalleled experience both domestically and abroad as well as the impressive depth and breadth of their internal resources. More than Lean consulting, Campbell could also provide concept design, cost projections, and feasibility models to help justify potential options and guide INFICON to the best solution.
INFICON is a leading provider of innovative instrumentation, critical sensor technologies, and advanced process control software that enhance productivity and quality in sophisticated industrial vacuum processes. Their analysis, measurement and control products are essential for professionals across industries including HVAC/R and automotive and equipment manufacturers who fabricate semiconductors and thin film coatings for a variety of products. Additionally, INFICON is an invaluable partner to defense departments worldwide leveraging their expertise in vacuum technology to provide unique, toxic chemical analysis products for emergency response, security, and environmental health and safety.
Lean Operations Assessment Offers Improvements
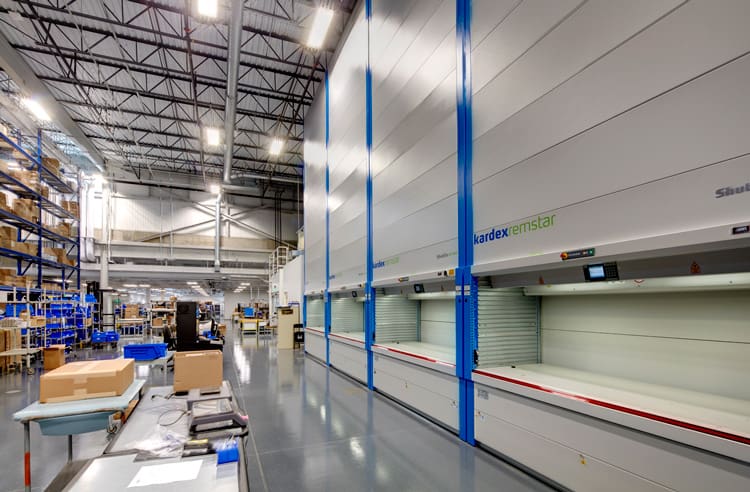
Working in close collaboration with INFICON’s vice president of operation, Stephen Chabot, and his team, Campbell Corporation began their process by completing an in-depth assessment of the existing INFICON facility. Seeking the input and insights from a broad cross-section of INFICON employees, Campbell learned not only INFICON’s future goals and objectives including that the production space for the manufacturing plant relocation and expansion MUST be flexible.
Campbell Corporation was able to offer valuable recommendations for operational improvements and flexibility through observation and application of various Lean manufacturing tools. Functioning as an unbiased third-party, Campbell’s combined experience in Lean manufacturing, real estate development, architectural design, and construction oversight offered a fresh perspective and insights based on their years of experience.
In addition to touring the existing Syracuse facility, Campbell also conducted site visits at INFICON facilities located in other regions of the world. Through these site visits, Campbell was able to incorporate the best processes and systems from INFICON’s various facilities together under a single roof in their plans for the new facility. The outcome of the site visits and facility assessments was a smart, flexible and detailed factory layout that would serve as the foundation for all solution options. By planning the new facility from the inside out, it was ensured that all solution options presented would encompass all necessary specifications and be designed around flexible Lean manufacturing principles.
Stephenn Chabot
VP of Operations
INFICON
As a valuable member of the team, Campbell Corporation brought a wide breadth of experience and expertise in planning, Lean manufacturing, and construction management to the project. In my experience working with other consulting parties, Campbell took a much more collaborative approach to managing the project which made them very easy and enjoyable to work with.
Campbell Corporation Identifies Feasibility and Solution Options
Armed with the findings and recommendations of the planning and assessment phase, Campbell began developing unique solution options for the flexible design, build, and construction of the new facility and costing out financial and logistical feasibility. Part of this process included working with INFICON in identifying and qualifying for a series of financial incentives, grants, and tax rebates that would help fund and quantify the construction of the new facility. INFICON had established a valuable network over the years and took the lead in procuring the incentive package. However, with years of experience in applying for grants and the information required for submittals, Campbell supported INFICON throughout the process.
Campbell developed capital and implementation cost projections as well as detailed site plans and design renderings for consideration that projected the feasibility of each option. By quantifying every step of the process, Campbell built a case for each solution option to help INFICON determine which would make the most financial and operational sense from both a short-term and long-term perspective. Ultimately, three options were presented to INFICON’s board: the first solution option proposed building the facility on a completely new site, the second recommended demolishing a portion of the existing facility and rebuilding on the same site, and the third offered an option of renovating the existing building and adding a new expansion. Through detailed analysis, the option that maintained the current buildings and expanded the footprint of the building on INFICON’s existing site was the best option.
Selecting the Right Team for the Manufacturing Plant Relocation
Recognizing Campbell’s breadth of experience and the knowledge gained of the company’s vision for the project through the feasibility and planning stage, INFICON invited Campbell to stay with them through the construction of the facility as their owner representative.
As INFICON’s owner representative, Campbell led a two-stage interview, proposal, and selection process to form the design and construction team that would execute the project. In the selection process, Campbell returned to vendors who had provided initial figures and cost projections during the feasibility phase to provide firm proposals for the chosen plan. However, when recommending the team, Campbell knew that the recommendation needed to be based on more than just price alone, but also each team member’s ability to understand the vision for the project and work collaboratively to make it a reality. Comprised of an architect and a team of contractors and engineers, Campbell recommended the final team based on their stellar reputation and unique qualifications that made them the clear choice for this project.
INFICON agreed with all of Campbell’s recommendations, and together defined the best contractual business relationship of each team member focusing on complete visibility of team member costs and profit centers and conducting final negotiations to assure INFICON is getting the best value throughout the duration of the project.
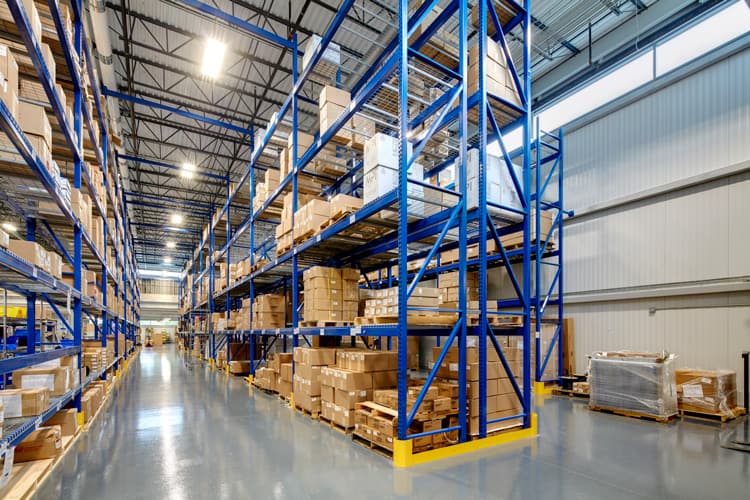
Setting the Pace

With a design team in place, Campbell was prepared to take everyone with them on the journey to complete the facility. Armed with the plans, specs, and figures prepared during the feasibility stage, Campbell was able to provide each member of the consultant team with valuable insights and background that they could leverage to offer design and construction recommendations for chosen solution option.
Throughout the engagement, communication and collaboration were cornerstones to the success of the project. Coming together weekly, each part of the project was discussed to check against the budget, quality standards, and overall project goals. Campbell Corporation was able to deliver a quality facility on time and on-budget outcome that met all of INFICON’s expectations and goals.
Unknown Unknowns
However, as with any construction process, the INFICON project was not without challenges. Land issues and concerns were among the largest hurdles that Campbell helped INFICON navigate. For example, the plans for the new facility called for INFICON to expand onto an undeveloped area of their owned property which had not been maintained for some time. The unmaintained state of the land necessitated navigating environmental issues including protected species which were successfully addressed with various government agencies. Campbell’s knowledge and experience in real estate development brought light to an unknown (and potentially project delaying) issue.
A second issue that Campbell helped INFICON overcome was the development of their new parking lot, which was planned for an area of their property that would require obtaining a permanent easement from the local utility company. As experienced real estate developers, Campbell was able to work collaboratively with INFICON and the power company through a series of detailed contract negotiations to gain the necessary permissions to build the parking lot and keep the project on schedule.
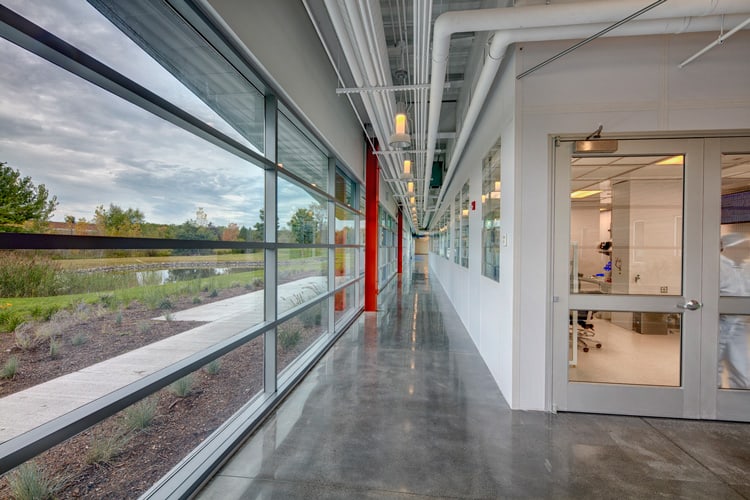
Clean Rooms


Among the most challenging and unique aspects of the INFICON project and their manufacturing plant relocation was the planning, design and construction of their world-class clean rooms. Complete with their own atmospheres and HVAC systems, the clean rooms were built essentially as a second building within their new facility. Due to the complex processes and requirements necessary to successfully design and build a clean room, a highly detail-oriented planning and design approach was deployed to ensure every aspect of the rooms were well thought out and tested prior to their final construction.
Using powerful BIM technologies, a three-dimensional rendering of the proposed clean room layout was created enabling INFICON’s team to virtually walk through the design as it was being planned and fully visualize the space. While the BIM modeling certainly offered INFICON a detailed look at the proposed plans for their new clean rooms, we took it a step further.
In constructing clean rooms it’s important to look at the project from all angles and at every level. It needs to be viewed at 50,000 feet, but also up close and personal. For this reason, a full-scale model of a partial clean room was built. While BIM technology-enabled INFICON to visualize the clean rooms, the model enabled them to experience the clean rooms before they were built. The clean room model served as a testing ground for all materials and technologies that would go into the construction of the space. Recognizing that in many cases the individuals who work in a clean room do so for extended periods of time throughout their workday, Campbell and INFICON wanted the environment to not only be flexible and efficient, but as pleasant as possible.
One area that was considered was the fans that run continuously to filter and circulate air within the clean rooms. Typically, these fans are rather loud and can be distracting and unpleasant to be near for extended periods of time. Using the model clean room, Campbell and INFICON were able to bring in a variety of fans to test and consult directly with the employees who would be working within the clean rooms. Going through this process for the fans and several other components enabled Campbell to select materials and components that would work for INFICON’s needs long term—saving them from costly renovations in the future and optimize the productivity of the employees upon completion.
Vince Nicorta
LEED AP BD+C Architectural
Partner
QPK Design
Working alongside Campbell Corporation as their partner on the INFICON project was like creating a fine Swiss watch. Campbell’s team expertly planned and flawlessly crafted the inner workings of the facility and then working collaboratively with us as the architect, we designed the environment that housed it.
Campbell Corporation Delivers Results Under Budget and Ahead of Schedule
The project’s successful completion was a true testament to the value of the planning and feasibility stage of the project. By having a well-thought-out and thorough plan in place to guide the project, the tone and expectations were set for all team members moving forward.
Working together with consistent communication and close collaboration, the team was able to complete the facility under budget and ahead of schedule. The ability to move the project forward quickly provided great advantages to INFICON both operationally and financially. Among the project’s greatest success was the efficiency of the construction process which was completed just 11 months after breaking ground and with very little downtime during the transition to the new space.
Today, INFICON’s world-class Syracuse facility is a benchmark for Lean manufacturing. This innovative facility provides new and flexible space, allowing INFICON the ability to maximize efficiencies throughout their processes and leverage the facility to promote the future growth of their business.
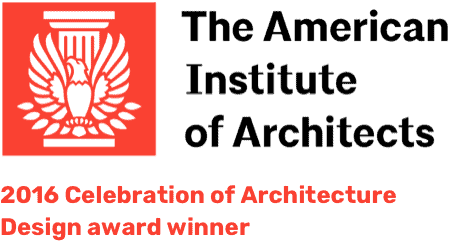

Ready to Improve Your Efficiency And Profitability?